Einstieg
BLENDING METAL POWDER: BLENDERS AND HANDLING COMPONENTS FOR YOUR PRODUCTION
Container Blender for Mixing Metal Powder
Additive manufacturing, or 3D printing, is a fast-growing industry that is fundamentally different from traditional manufacturing processes. It offers new opportunities for research and development as well as for industrial manufacturing companies.
Advantages of 3D Printing:
![]() |
Reduce manufacturing time |
![]() |
Reduce production costs |
![]() |
Reduced risk due to less expensive and shorter manufacturing process | ![]() |
Flexible customization of models |
![]() |
Design flexibility | ![]() |
Sustainability |
Metal powder mixing and processing, as well as efficient powder handling for metal additive manufacturing, are becoming increasingly complex. At the same time, there is a need to achieve an effective and cost-efficient process, especially in metal powder mixing, material flow and increasing automation.
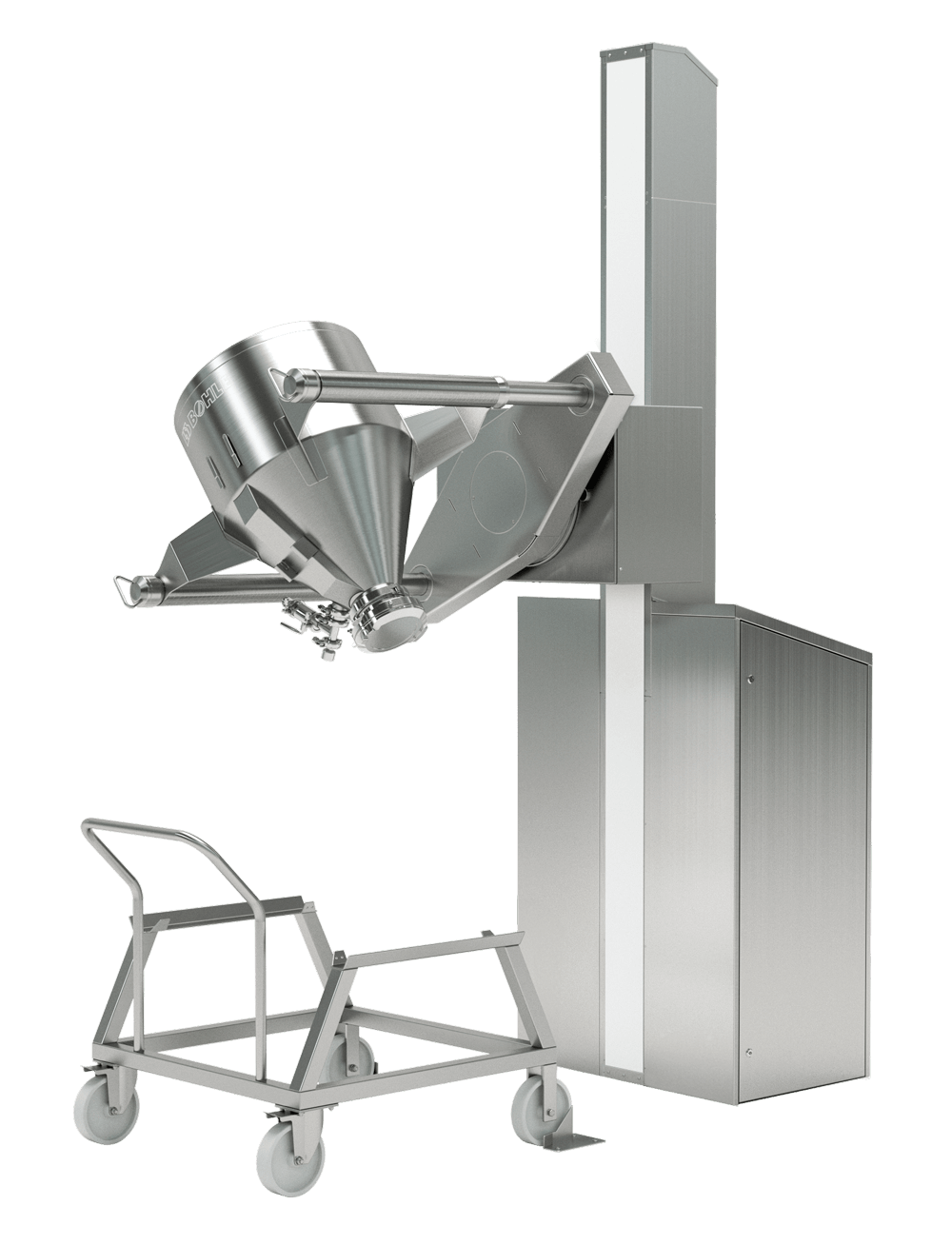
Unser Angebot für die Produktion von Metallpulver
L.B. Bohle: Our offer for the production of metal powders
L.B. Bohle manufactures modular and flexible systems for metal powder blending and material handling.
We offer systems for weighing, feeding, blending and storing metal powders for additive manufacturing. Our systems are modular and can be flexibly integrated into the 3D printing production process. With decades of process experience in the pharmaceutical, chemical and food industries, we have the expertise from several thousand projects.
Trenner Broschüre
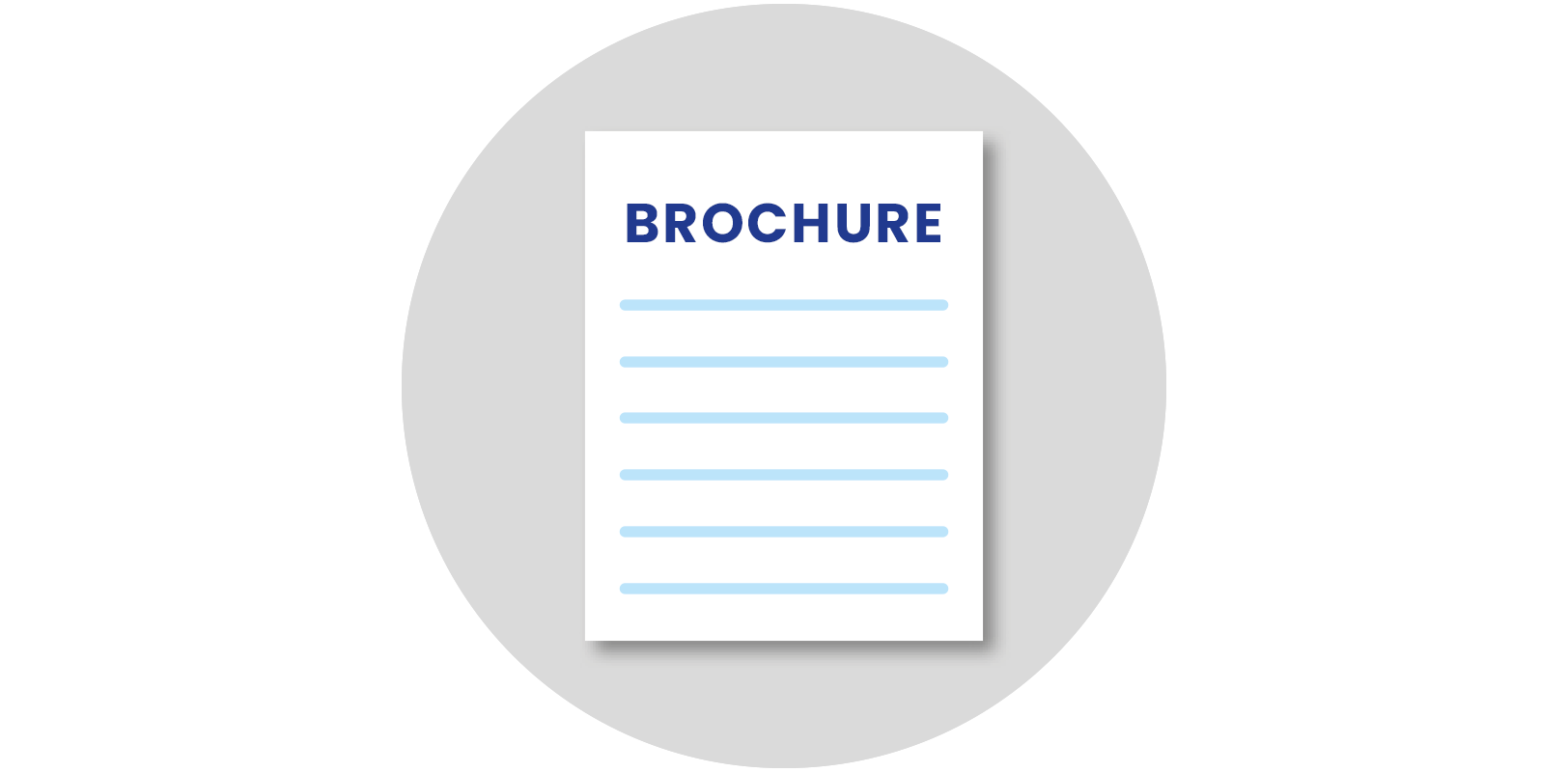
Perfekte Produktionsergebnisse beim Mischen von Metallpulver
Perfect Metal Powder Blending Results
In the blending process, further alloying elements and the lubricant for the subsequent pressing process are mixed in addition to the metal powders. At the same time, the blending container is inerted.
The special feature in the handling of metal powders is that the material can easily oxidize due to its chemical properties and fine grain size with a correspondingly large surface area. This high reactivity means that the mixing of the metal powders takes place in an inert atmosphere.
In this case, a gas (argon or nitrogen) is added to the blend to prevent an explosive atmosphere. The result of the blending process is a metal powder with the desired material properties that minimizes frictional forces during pressing.
Overmixing should be avoided when mixing metal powders, as it increases the bulk density of the mixture. In addition, overmixing reduces the green strength of the compacts. This reduces the proportion of metal-to-metal contacts, crucial for green strength.
The flow properties are also affected. Good flow properties of the powder are elementary for filling the die.
Metal powder properties:
Further processing of the metal powder is affected by the following powder properties
![]() |
Particle or grain size |
![]() |
Particle or particle size distribution |
![]() |
Particle or particle shape and structure | ![]() |
Surface texture |
Bulk density is an important parameter because it has a significant effect on the strength of the compact that can be achieved during compaction.
A broad particle size distribution is advantageous to allow a powder to be easily and densely introduced into the die. The spaces between the larger particles are effectively filled by the smaller particles.
Smaller particle sizes result in smaller pores that close more easily during sintering. A higher proportion of fine particles degrades the flow properties of the powder.
The purity of the powder is critical. The level of acceptable contamination depends on which components are present and in what form.
Jetzt testen – Nutzen Sie unser Service Center für Ihren Test
Test it Now: Use our Service Center for Your Test
Our test and development center in Ennigerloh (Germany) offers you optimal conditions for testing your products on our equipment.
Our team will be happy to answer any questions you may have about our products and technologies, and to assist you with on-site testing.
Optimize your production of metal powders for 3D printing with our machines and processes.
Make an appointment now!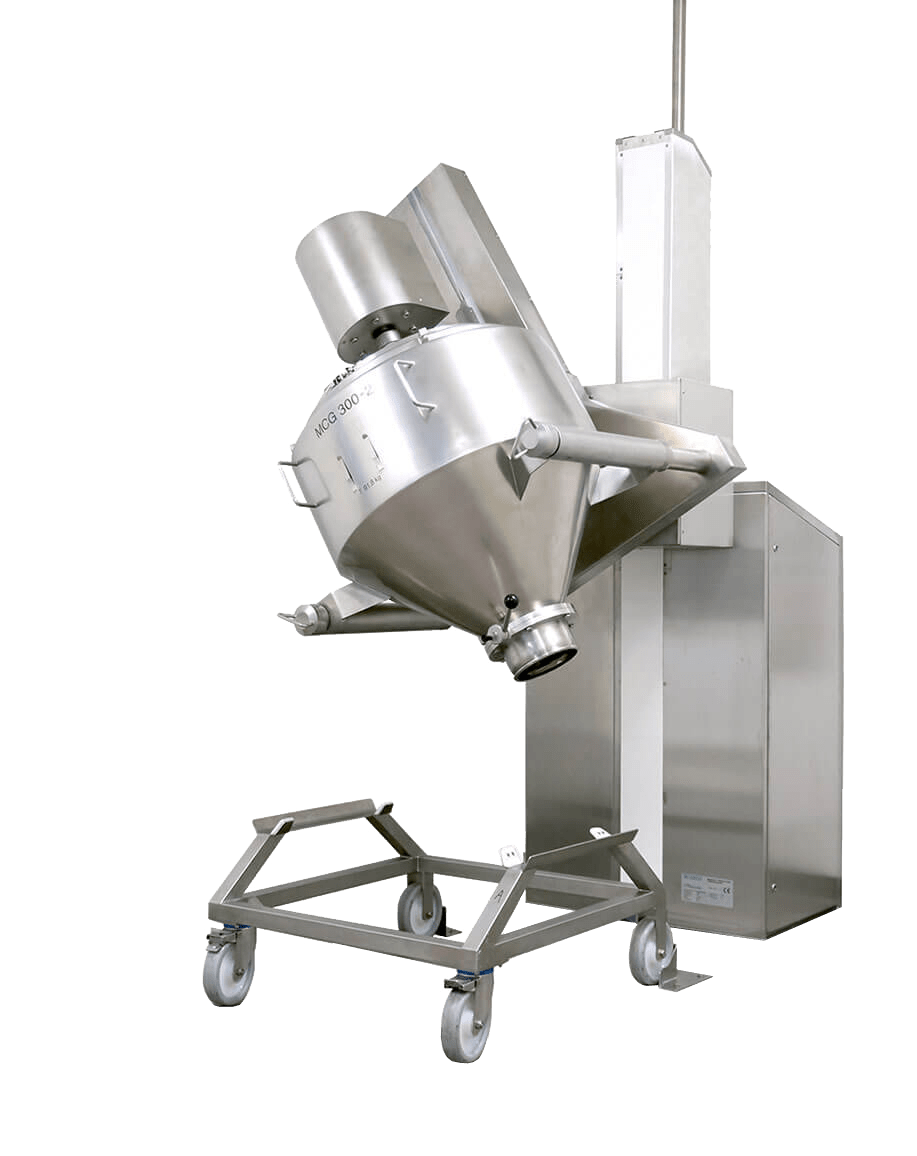
Das Unternehmen
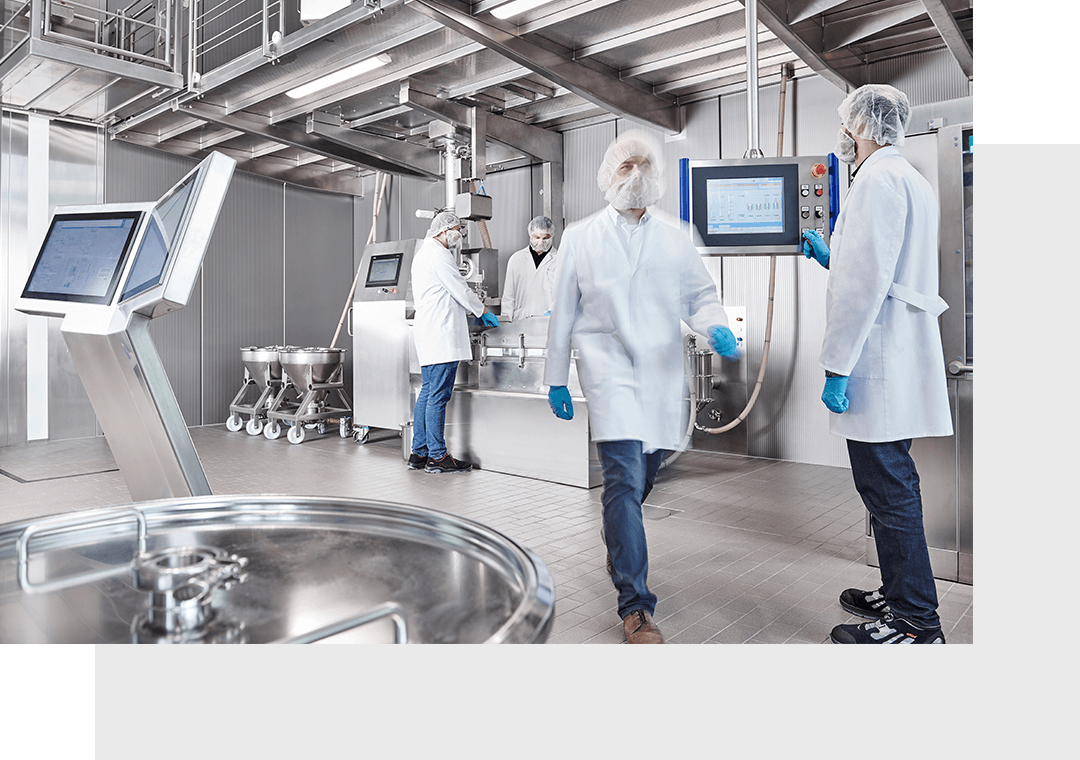
The Company
L.B. Bohle is a leading technology company for the pharmaceutical, chemical and food industries. Based in Ennigerloh, Westphalia, the company has been a reliable and respected partner to the industry for more than 40 years.
Our 300 employees produce high-quality, safe and environmentally friendly machines “Made in Germany”, which improve our customers’ production and simplify their processes every day.
Our service team supports customers worldwide from machine installation to maintenance and calibration.